Table of Content
Almost two years ago, we launched PubMed Journals, anNCBI Labs project. Drainage can play a large part in the amount of settling that can occur and something that should be addressed as part of the install and maintance. Dirt can and will settle even after being ” compacted” Which is a large portion of what would be described as settling. The relevel will allow for that assuming typical circumstances and no frost heaves, expansive soil or other ground issues. There are only a couple of websites that collect reviews on manufactured home dealers and builders.
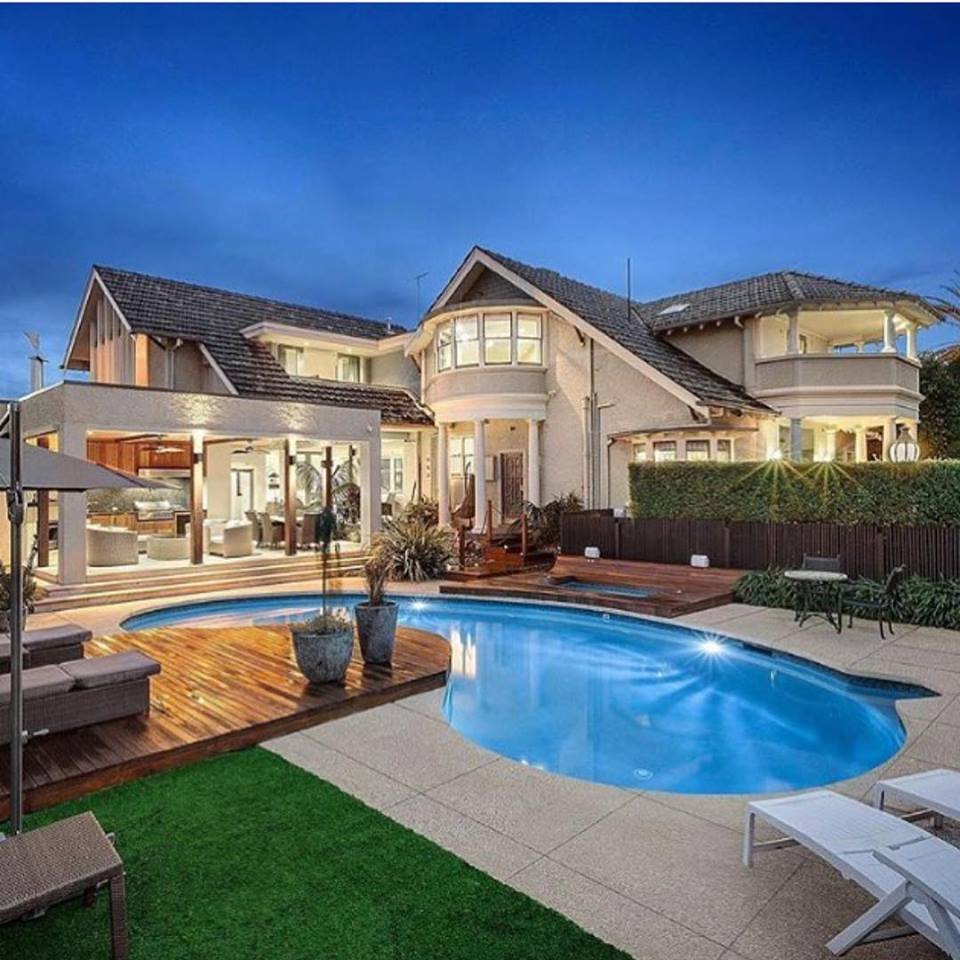
If it’s your dream of owning a home that has never been lived in and reflects your tastes, you’re a candidate to build a custom modular home. Modern modular construction creates homes that are beautiful both inside and out. In this age of automation, there are a number of benefits to this ultra-efficient building method. When you’re thinking about building a house, don't forget about planning out the cost of outdoor living space. The national average is about $7,670 for an outdoor living space, with a typical range between $4,150 and $11,190. The quality of the material you choose makes a big difference.
Timberland by Tiny House Building Company
For a while, he lived in Oregon, and that’s when the tiny home bug bit him. So when he returned to Hawaii, Hardin made it his mission to spread the glory of tiny living to his home state. You can select the size of the cabin, which is available between 10 and 20 feet, so it’s plenty sizable .
The fact that your home is being built in a prefabricated construction does not impact its foundation in any way. Therefore, the cost of your foundation will be the same as the cost of a foundation for a stick-built house. The average cost of a single-family modular house is between $100,000 and $150,000 for a prefab design. The cost of a custom single-family prefabricated house averages $240,000 to $460,000. The average size of a single-family home in the U.S. is just over 2,000 sq.ft.
Factors That Affect Your Home-Building Cost
Factory modular build homes can be constructed in a much shorter time frame than a conventional site built home. After the engineering plans have been approved and the home is scheduled for production it only takes a couple of weeks for the home to be ready to deliver to the site location. Simultaneously, while the engineering and the home construction is taking place, the developer or home owner can be doing the site preparations.
The cost of a building permit for a home is between $1,200 and $2,000. Permit costs can vary based on your location and the permitting requirements in your area. If you'd like to know the general price range of your dream build by size, take a look at these averages below.
We are excited to offer homes from Palm Harbor, Redman, and Prime homes now!
Modular homes have a better reputation overall, which can be seen by the fact that banks will mortgage them like a standard home. However, many people do not know the difference between a modular home and a mobile home, so they often get misconstrued. This has caused modular homes to also get a similarly bad reputation in some areas because of this mix-up. If you have questions about modular home building or want help determining which type of California modular home plan is best for you, please contact our team. Fredericksburg, Virginia’s Tiny House Building Company builds modular homes by the dozens. The variety of models offered is impressive, and each home is customizable to boot.
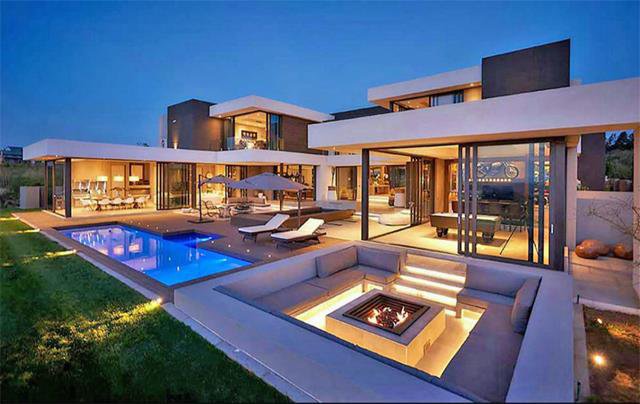
Most of the house building costs are in the cost of the base home. Depending on the house size and the company building it, much of the finishing work may be done at the factory, or it may all need to be done at the job site. The more pieces the house is delivered in, the more work needed to piece them together and button up the house. While a small house delivered in one or two pieces may be sided at the factory, a larger house will need to be finished and sided on-site. These details create a wide range of installation and finishing costs for your prefabricated house.
If there’s room in the budget after construction, you might be able to afford an interior designer or a landscaper. Plumbing, electrical, and HVAC make up most of your major system costs. If you buy land in a metropolitan setting, developers will most likely have finished the lot prior to listing it. The bigger the build, the more labor costs you should expect. A general contractor costs around 10%–20% of the total project. A house can be as large or as small as you want it to be, and it can also have as many or as few rooms as you need as well.
We decided to do a little bit of detective work to find the most expensive speakers ever made - and we've been blown away by some of the price tags. The majority of the items on this list would be beyond the reach of most customers, but there's no harm in ogling some gigantic shiny speakers with crazy tech inside them. On the other hand, you might be drawn to the mobility of a manufactured home. Modular homes are assembled on a site and anchored to a foundation, whereas a manufactured home is transported in one piece to a site and can be relocated.
A little dozer work and a french drain or two can remedy just about any kind of water or moisture issues on a site. I’ve seen manufactured homes installed in near swamps in SC but with the right grading and preparation, it was turned into a fine lot. Also, I know it is difficult or impossible in some cases to get financing to buy a manuf. Does stem wall construction, because it is also used for site-built homes, imply good financing options? This would be a consideration as we would eventually need to consider the resale value of the property. A modular home is constructed inside a factory controlled environment.

Because mobile homes are not technically permanent structures, they have different rules that govern their construction. Instead of abiding by local building statutes, mobile homes are beholden only to The US Department of Housing and Urban Development regulations. In fact, one of the easiest ways to tell if a home is a mobile home or a permanent structure is to look for the HUD tag that all mobile homes have to display by law. To keep the homes mobile, they are not put onto permanent foundations.
You also need to set aside space for fencing on your property line and where your home's utility grid will go. Besides square footage, the construction pros who build your house represent 30% to 50% of your project costs. As you might guess, the labor costs vary relative to the size of your house, your contractor's buying power, and their ability to get reasonably priced labor. The cost of customizing a base home averages $20,000 to $30,000. This is the cost of making moderate changes to a readymade plan. It is possible to choose a house plan and make no changes at all.
As true brick and mortar homes have shifted to this design style, many have assumed that modular homes lack custom designs, and will fall into a cookie-cutter style as well. However, these are common misconceptions around modular builds and how they differ from true custom designs. In today’s world of subdivisions and mass production, new home construction lacks a lot of the custom features most home buyers crave. Home design comes off as cookie-cutter, and plug and play.
Modular homes must adhere to all local and state building codes, while mobile homes only have to meet the HUD codes. Modular homes are built in a controlled environment protected from weather out of the best building materials. Constant quality control checks and third party inspectors ensure that your home is precision built and in compliance with all codes. Each of our modular pod designs is built entirely in our Gold Coast factory meaning we don’t experience the delays that are typically faced by traditional onsite builds. Not only is our factory manufacturing process far more efficient, but it also affords us the freedom to ship anywhere in the country.
Buying or selling a home is one of the biggest financial decisions an individual will ever make. Our real estate reporters and editors focus on educating consumers about this life-changing transaction and how to navigate the complex and ever-changing housing market. From finding an agent to closing and beyond, our goal is to help you feel confident that you're making the best, and smartest, real estate deal possible. Browse our Homesand view the fantastic styles and floorplans of our Wisconsin Homes, Highland Homes, and Commercial Buildings. Luckily, you don’t have to be a light bulb expert, manufacturer, or know one to check the energy efficiency. Hurricane straps and ties help keep your roof from blowing off in high winds and can prevent your house from collapsing if the walls are damaged.
No comments:
Post a Comment